
Wie funktioniert PLUCC?
Das PLUCC Verbindungssystem besteht aus mindesten zwei Bauteilen, die formschlüssig ineinandergesteckt und dann mit einer schraubartigen Verbindung entsprechend der notwendigen Steifigkeit verbunden werden.
Das System ist dann sofort einsatzfähig und hält allen zuvor ausgelegten Lastfällen stand.
Für den Fall einer Demontage kann das Stecksystem ohne Steifigkeitsverlust wieder auf den Originalzustand montiert werden.
Es können prinzipiell beliebige Bauteile unterschiedlicher Topologie je nach gewünschter Karosserie zusammengesteckt werden.
PLUCC-Verbindungs-Systeme können als Baukasten verstanden werden, wobei einzelne Baugruppen gegebenenfalls aus austauschbaren Bauteilen mit PLUCC-Verbindung aufgebaut sein können.

Technische Einsatzbereiche
PLUCC findet aber nicht nur im Fahrzeugbau seine Anwendung sondern kann überall dort eingesetzt werden, wo entweder schnell lösbare oder einfache Verbindungen von Elementen oder Baugruppen gefordert sind.
Eine solche Anforderung kann beispielsweise im Hochbau oder Brückenbau bestehen.
Dort können mit Hilfe von PLUCC vormontierte Baugruppen mit wenigen Arbeitsschritten aneinander gefügt werden.
Für den Brückenbau wäre das System für das Zusammenfügen von stabförmigen Bauteilen als auch für Fahrbahnsegmente denkbar.
Die Dimension der Verbindungselemente wird den zu verbindenden Bauteile angepasst.
Im Fall von Fahrbahn-Segmenten für eine mehrspurige Brücke können die Verbindungsteile Kubikmeter große Abmessungen annehmen.

Einsatz der 3D-Drucktechnik für die Produktion
Die Anwendung der 3D Druck Technologie für PLUCC wäre ideal, ist aber auch nach neuesten technischen Stand derzeit nur eingeschränkt für einzelne Bauteile nutzbar.
Mit dem Einsatz des 3D Drucks würde die Anwendung des PLUCC-Systems eine noch höhere Flexibilität erreichen.
Zur Verifizierung der PLUCC-Technologie hat die 3Pman GmbH ein 3D-Druck-Modell anfertigen lassen, um grundsätzliche Funktionen sowie Montage-Handling als auch Strukturbelastungen zu prüfen.
Es wurden speziell verschiedene Lastfälle untersucht, um Aussagen bzgl. unterschiedlicher Topologie zu erhalten.
Der Video-stream zeigt einen kleinen Ausschnitt ausgewählter Lastfälle.
Die weiteren Abbildungen des 3D-Druck-Modells zeigen das exemplarische Design, das bis heute weitere Entwicklungsschritte durchlaufen hat.
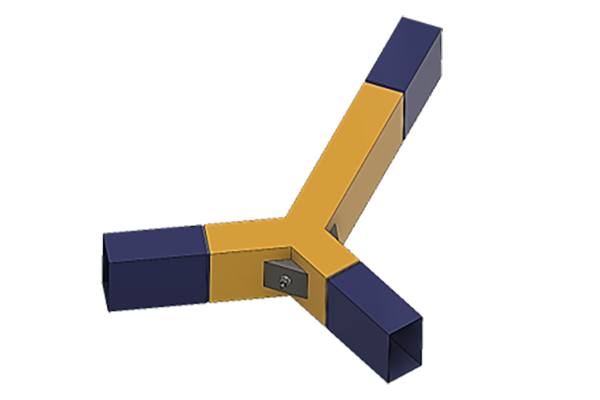
PLUCC-Struktur-Knoten
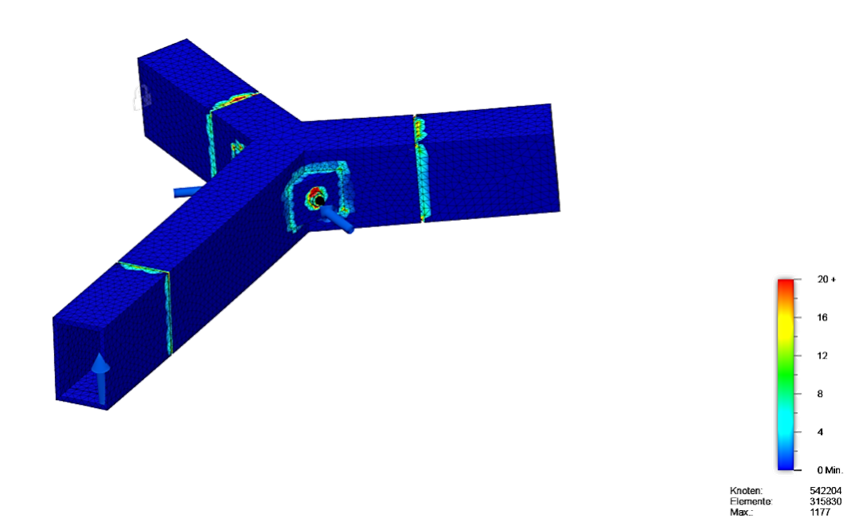
Kontaktdruck unter Betriebslast
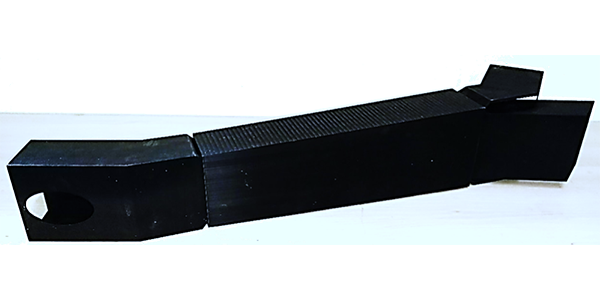
PLUCC- 3D-Druck-Versuchsträger
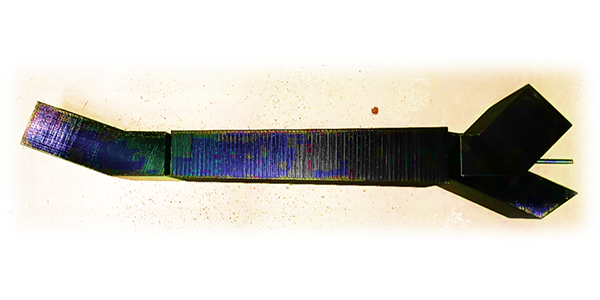
PLUCC- 3D-Druck-Versuchsträger
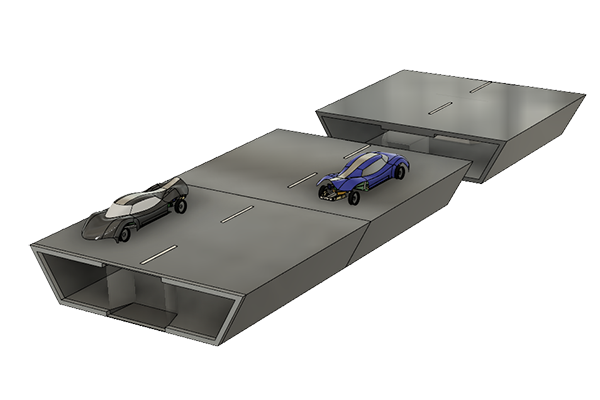
PLUCC-Brücken-Konzept
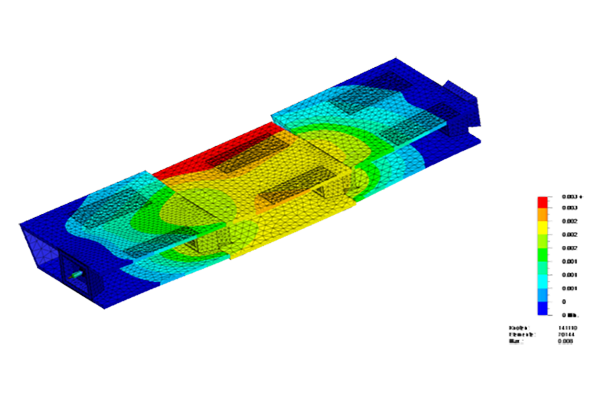
Berechnungsergebnisse unter Betriebslast
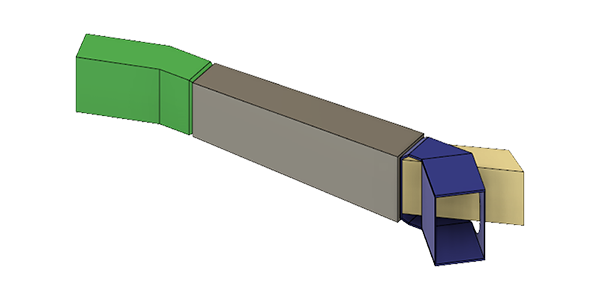
CAD 3D-Druck-Modell

CAD 3D-Druck-Modell

Material - Design
Um große Bauteile mit überschaubarem Aufwand auf Baustellen am Boden oder im Hochbau bewegen zu können, sollten diese möglichst leicht sein.
Das PLUCC-Verbindungs-System kann aus metallischen als auch Faserverbund-Materialien konstruiert werden, wobei einzelne Bauteile wiederum Werkstoff-Kombinationen aufweisen können.
Das bedeutet, dass durch konstruktiven als auch Material-Leichtbau die Verbindungs-Elemente bzgl. Masse deutlich reduziert werden können.
Hierbei können Kunststoff-basierende Werkstoffe mit geeigneten Metall-Werkstoffen kombiniert werden.
Das hat zur Folge, dass Maßnahmen zur Erhöhung von Steifigkeit und Festigkeit umgesetzt werden müssen.
Dabei müssen schlanke Tragwerke gegen Beulen und Knicken ausgelegt werden, bei konzentrierten Krafteinleitungen hingegen müssen Spannungsspitzen vermieden werden.
Dazu kann man Leichtbaukennzahlen ermitteln, die für spezielle Belastungsfälle das auf die Dichte bezogene günstigste Material ermitteln.
Hier erreichen die Faserverbund-Werkstoffe meist die besten Werte, kommen aber aufgrund der hohen Kosten oft nicht in die engere Auswahl.
Ebenso nimmt Korrosion eine nicht zu unterschätzende Rolle in die Überlegungen bei der Materialauswahl ein.
Der Fortschritt der korrosionsbedingten Schwächung der Struktur bestimmt ebenso Wartungsintervalle, die möglichst groß sein sollen.
Der Zugang zu korrosionsanfälligen Bereichen muss zu Beginn der Entwicklung bedacht werden, um nicht in kostspieligen Reparatur-Maßnahmen zu enden.

Konstruktions - Prinzipien
Auch wenn die Verwendung leichter Werkstoffe genutzt wird, müssen konstruktiv Lösungen erarbeitet werden, die die oben genannten Bedingungen gegen Versagen erfüllen.
Um Leichtbau effizient gestalten zu können, müssen mehrere konstruktive Grundprinzipien beachtet und umgesetzt werden.
- Vermeidung ungünstiger direkter Krafteinleitung und die Wahl direkter Lastpfade, um unerwünschte zusätzliche Momente zu vermeiden
- Wenn möglich großflächige Lasteinleitung wählen, z.B. bei einer Querlast auf Profile. Damit wird die maximale Verformung als auch das Biegemoment deutlich abgemindert
- Abtragen von Quer-Lasten auf direkt darunter liegenden Lagern (Stützen). Damit lässt sich das Biegemoment ggfls. auf Null reduzieren
- Wahl von geschlossenen Profilen ist gegenüber offenen Profilen vorzuziehen. Dies gilt vor allem bei Torsions-, aber auch bei Querkraft-Belastung außerhalb des Profil-Querschnitts. Das geschlossene Profil ist deutlich torsionssteifer. Zudem liegt der sogenannte Schubmittelpunkt innerhalb des Profil-Querschnitts und verhindert dadurch ein zusätzliches Torsionsmoment
- Wahl von Hohlprofilen bei Querkraft-Belastung gegenüber Vollprofilen günstig, da sich die gegen Biegeverformung wirkenden Trägheitsmomente so weit wie möglich vom Flächen-Schwerpunkt befinden sollen. Andererseits übernehmen die Stege des Profils den bei der Biegung auftretenden Schub
- Auf ähnliche Weise lässt sich Plattenbiegung reduzieren. Hier sollte die auf Querkraft belastete Platte zwei Deckhäute aufweisen, zwischen denen sich ein Kern befindet